Rocking Bioreactor Systems
Basic BioRocker System
Benefits of the Basic Biorocker System
Functionally Closed System
Reduces contamination risks, ensuring safe and reliable cell culture processes essential for clinical and research applications.
Automated Process Monitoring
Remote control capabilities with automated alerts and customizable settings allow for efficient and reliable bioprocess management, saving time and reducing manual oversight.
Regulatory Compliance
Designed to align with GMP standards and 21 CFR Part 11 compliance our rocking bioreactor provides confidence in navigating stringent regulatory requirements.
Basic BioRocker Details & Technical Data
The Basic BioRocker provides a closely monitored and highly controlled environment for the growth of viable cells to densities suitable for various applications, process development, and clinical manufacturing operations. Its flexible design accommodates various cell types and culture conditions by adjusting the rocking platform’s motion, speed, and angle. Ideal for both suspension and adherent cultures, the Deluxe BioRocker supports processes including cell culture expansion, fermentation, cell therapy, gene therapy and bioprocessing & manufacturing. The functionally closed system minimizes contamination risk, and automated process monitoring with remote control capabilities ensures precise and efficient operation.
- Rocker Speed: 2 to 30 rocks/min ±1 r/min
- Rocker Angle: 2° to 12° ±1.5°
- Tilt Motor Operational Temperature: 0° to 85°C
- Tray Heater Operational Temperature: 0° to 60°C
- Tray Heater Power Consumption: 250 W
- Temperature Element Operating Range: -50°C to 200°C ±0.2°C
- Vent Filter Heater: User Configurable Duty Cycle
- Total Load Cell Capacity: (3) Load Cells: 150 kg | 330 lbs*
- Load Cell Safe Load Limit: 200% Emax*
- Load Cell Side Load Limit: 100% Emax*
- Load Cell Accuracy: ±1% of readings in net weight working range of 0 to 20 kg*
- Power Supply: U.S.: 110 to 120 VAC, 60 Hz, 6.7 A; International: 230 VAC, 50 Hz, 3.4 A
- Power Consumption: 804 W
More details are available in the technical brochure.
Elevate your bioprocessing with AES Rocker Bags, featuring advanced spot sensors for precise monitoring. Available in 20L and 50L volumes, these bags integrate seamlessly into your workflow with convenient disc port connectors. Sterilized via gamma ray radiation and packaged in double-layer PE vacuum bags, they ensure unmatched sterility and purity. The cutting-edge CellBios CSF51 film structure offers excellent clarity and transmittance, while compliance with ISO and USP standards ensures safety and reliability. Ideal for scientists, engineers, and procurement decision-makers, AES Rocker Bags deliver exceptional performance and reliability in a Class 7 Clean Room environment.
- Film Material: CellBios CSF51: Ultra-Pure PE/EVOH//Ultra-Pure PE (liquid contact layer)
- Environmental Requirement: Class 7 Clean Room Environment
- Film Thickness: 0.325 mm ±0.05
- Bag Volume: 20L or 50L
- Sterilization Method: Gamma Ray Radiation (25 – 40 kGy)
More details are available in the technical brochure
The Deluxe BioRocker is designed to meet the rigorous demands and standards required in regulated environments. It is GMP compliant and can be incorporated to meet 21 CFR Part 11 compliance regulations.
The AES Rocker Bags used with the system adhere to stringent quality and safety standards, including ISO 10993 and USP testing for hemolysis, cytotoxicity, pyrogen, implantation, irritation, systemic toxicity, bacterial endotoxins, particulates, microbial immersion, and biological reactivity. This ensures the highest levels of safety and reliability for biopharmaceutical applications.
Explore the key features of the Basic BioRocker System
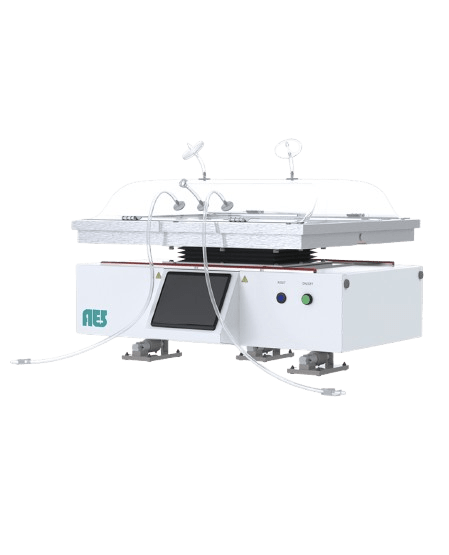
Integrated Load Cells (Optional)
AES Rocker Bag
HMI Screen (Optional)
Choice of Small
(10L to 20L) or
Large Tray (20L to 50L)
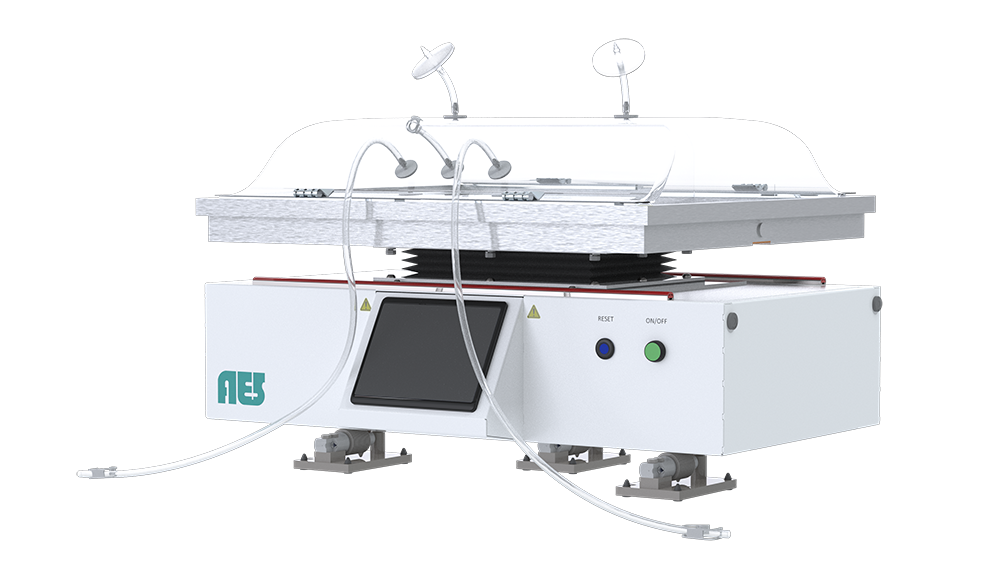
Integrated Load Cells (Optional)
AES Rocker Bag
HMI Screen (Optional)
Choice of Small (10L to 20L) or Large Tray (20L to 50L)
Why Choose AES for Your Rocking Bioreactor System?
Customizable for Your Bioprocess Needs
The Basic Biorocker can be tailored to meet the specific requirements of your bioprocess. Whether you need custom sizes, configurations, or features, we work closely with you to ensure this rocking bioreactor system aligns with your needs.
Seamless Integration for Your Lab or Facility
The Basic BioRocker is designed for seamless integration with your DCS. This compatibility allows for easy connection and communication with existing automation and control systems, enabling centralized monitoring and control of your operations.
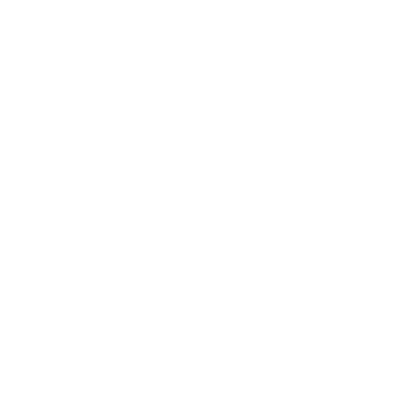
Aftermarket Services & Training
Comprehensive aftermarket services and training is available to ensure you get the most out of your rocking bioreactor system. Our team provides ongoing support, maintenance, and training to keep your operations running efficiently and effectively.
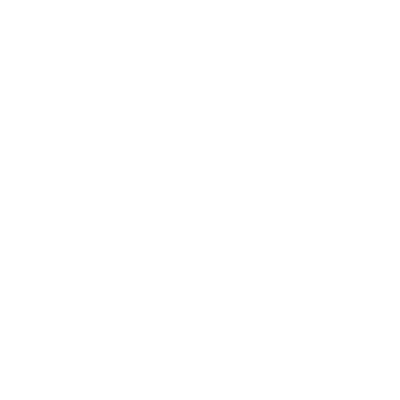
Fabricated in the USA
All rocking bioreactor systems are manufactured in the USA, adhering to the highest standards of quality and precision. This ensures reliability and consistency in every unit, providing you with a dependable solution for your bioprocess needs.
Think AES for Your Rocking Bioreactor Needs
Basic Rocking Bioreactor Applications

Cell Culture & Fermentation
- mAb
- Vaccine Production
- Antibodies
- Recombinant Proteins
- Cell-Based Meat
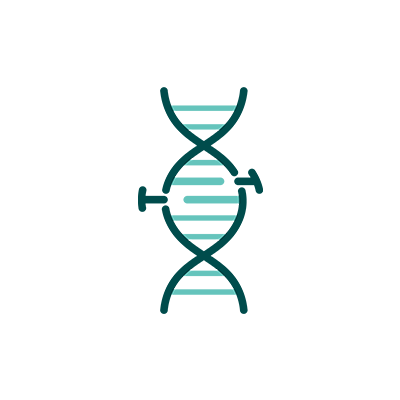
Gene
Therapy
- AAV
- Gene Replacement
- Gene Editing
- Oncolytic Viruses

Cell
Therapy
- CAR-T Therapy
- iPSC
- MSC

Bioprocessing & Manufacturing
- Media & Buffer Prep
- Upstream Processing
- Scale-up & Scale-down
- Process Development

Frequently Asked Questions
Below are answers to some of our most common questions about the Basic Biorocker. Whether you’re looking for detailed specifications, customization options, or insights into how this rocking bioreactor integrates into your bioprocess, we’ve got you covered. If you have any further questions, please don’t hesitate to contact our team.
Yes, the Basic BioRocker is highly customizable to accommodate specific process requirements. Our team collaborates closely with clients to tailor the system, optimizing it for unique cell culture and bioprocessing protocols.
Absolutely. The Basic BioRocker integrates with Rockwell as a standard. However, our engineering team can customize the integration to seamlessly work with your preferred DCS, ensuring compatibility and streamlined operation within your existing automation infrastructure.
Certainly! At AES, we conduct rigorous Factory Acceptance Testing (FAT) to guarantee that all equipment meets our stringent quality standards before it leaves our facility. In addition to FAT, our dedicated Global Service Team can oversee Site Acceptance Testing (SAT) to ensure seamless installation and operation at your site. For more detailed information, please visit our Aftermarket Service page.
Yes, in addition to detailed user manuals, we can provide comprehensive operator training sessions. Our training ensures your team can confidently operate and maintain our equipment, maximizing its performance and longevity.
Yes, we do. Our Global Service Team is unwaveringly dedicated to providing comprehensive aftermarket support to ensure your equipment continues to operate at peak performance. For any issues that cannot be resolved remotely, we guarantee on-site arrival within 48 hours. For more details, please visit our Aftermarket Service page.
Lead times vary depending on the complexity and customization requirements of the equipment. Our sales team can provide specific lead time estimates based on your project timeline and needs.
We can provide references upon request. These documents showcase our successful collaborations and the positive impact of our solutions on our clients’ operations.
Get A Rocking Bioreactor System that Meets Your Specific Bioprocess Today!
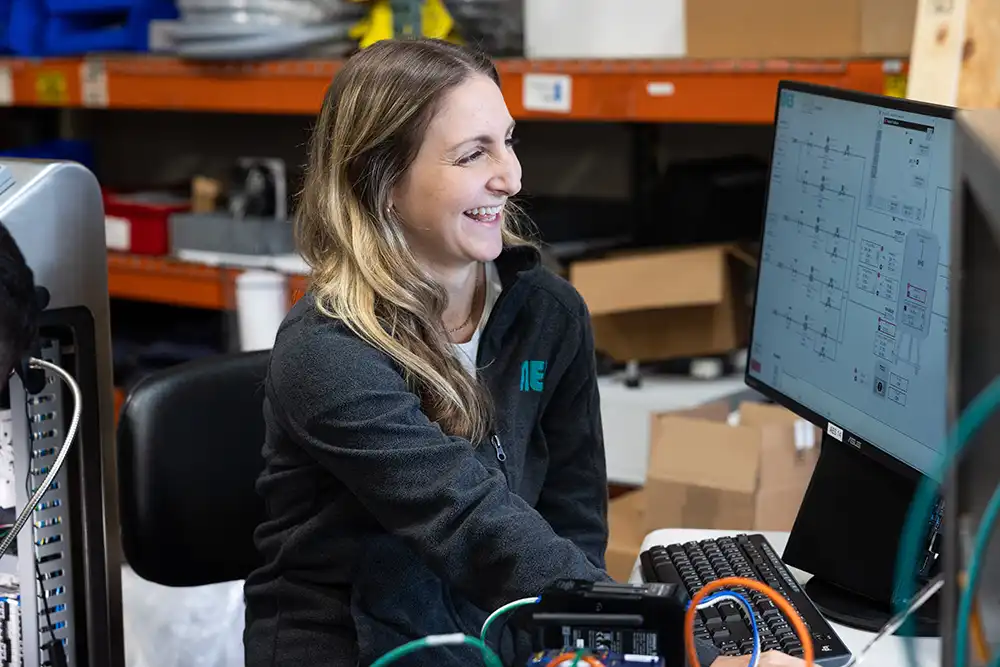